Knowing what kind of control system to use: that’s a question that must be answered before setting up the factory floor. Why would someone choose pneumatic over electrical controls?
In industrial automation, electrical and pneumatic systems are commonly used for moving loads. These systems exhibit numerous advantages, share common features, and execute comparable tasks. This comparison calls for an evaluation of their strengths so system developers can make an educated decision when deciding which is most suitable for their application.
Comparing Electrical and Pneumatic Systems
To begin, here is a brief summary of several of the main criteria that set these two systems apart from each other.
Advantages of Electrical Systems
Precision: Electrical systems offer high precision, making them ideal for tasks that require accuracy.
Speed:Electric actuatorscan achieve high speeds, enabling rapid and efficient operations.
Control: Fine control over power delivery allows for intricate adjustments in movement and operation.
Integration capabilities: Electrical systems integrate well with advanced automation technologies for enhanced connectivity and control.
Advantages of Pneumatic Systems
Durability: Pneumatic systems are robust and durable to withstand harsh industrial environments.
Cost-Effectiveness: Pneumatic systems often have lower upfront costs, making them economical for certain applications.
Simplicity in maintenance needs: Pneumatic components are often simpler and easier to maintain, resulting in cost-effective and straightforward upkeep.
Noise immunity: Electrical equipment that disturbs high-speed voltage signals does not affect air motion.
What are Electrical Systems?
An electrical control system, in our current context of motion control and loads, encompasses the utilization of electrical signals through devices to manage and regulate the operation of machinery or processes. These electrical signals provide precise control over movements. Electrical systems are favored for their accuracy, speed, and integration potential.
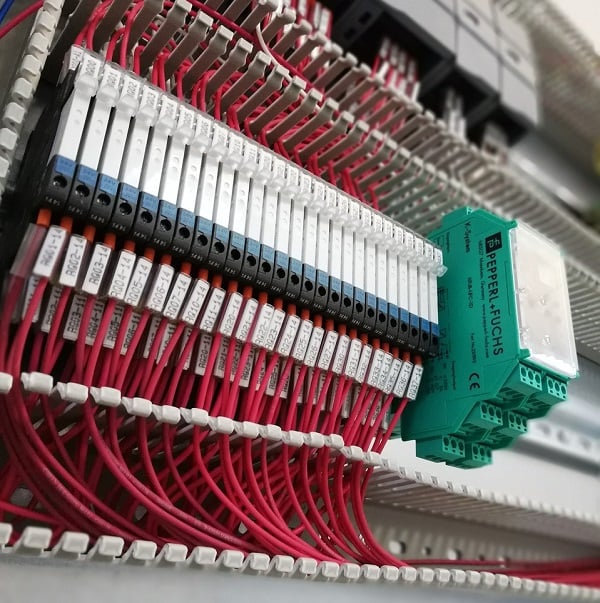
Inside a wired control cabinet
Figure 1.An example of wiring for electrical controls. Image used courtesy ofPixabay
What are Pneumatic Systems?
Pneumatic systems use compressed air to control the movement and functionality of various components. Key elements commonly include air compressors, valves, cylinders,and air-powered motors. These components provide robust and reliable control when used properly. Pneumatic systems are often recognized for their durability.
Hydraulic systems are a close relative of pneumatics, but for the sake of this article, only the pneumatic systems will be considered, as they do have many unique characteristics.
Energy Source: Electricity vs. Air
Electrical and pneumatic control systems have differences in their source and conversion processes. Electrical systems draw power from electrical sources. It then translates into mechanical energy through devices like electric motors. The precision in electrical systems originates from the consistent and predictable nature of the energy conversion process. This makes electrical systems suitable for tasks requiring intricate control. Each component in the motion process must be supplied with electricity, from the switches and controllers to the final load device.
In contrast, pneumatic systems derive energy from compressed air stored in reservoirs, releasing it to generate mechanical energy. Compressed air is less susceptible to environmental factors such as moisture and temperature variations. Also, the process of translating compressed air commonly involves simple and robust mechanical components such as cylinders. These components are known to endure heavy-duty use and withstand the stresses of demanding applications. Pneumatic systems have resilience in challenging environments, and the only input electricity demand is for the compressor, which may provide distributed air to many remote components without needing any further electrical infrastructure.
The choice between these systems pivots on the specifications needed for the application. Electrical systems excel in precision and predictability, while pneumatic systems thrive in harsh demanding conditions.
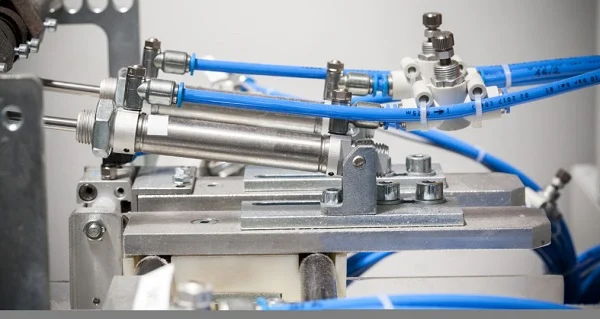
Pneumatic valves, tubes, and cylinders
Figure 2.Pneumatic cylinders equipped with flow control valves to perform controlled mechanical movement. Image used courtesy ofGlobal Electronic Services
Conductors: Wires vs. Pipes and Tubes
The distinctions between electrical and pneumatic systems extend to their modes of transmission through conductors. Electrical systems use wires to efficiently carry electrical power to various components. Wires, typically composed ofhighly conductive materialssuch as copper offer a low resistance to the flow of current. This low resistance results in minimal loss and delay during transmission, ensuring swift and reliable communication within electrical systems. However, high-frequency signals can be more susceptible to inductive noise and loss of precision.
In contrast, pneumatic systems employ hoses to transmit compressed air. Unlike the nearly instantaneous transmission of electrical signals through conductors, the compressibility of air in hoses introduces a lag in response during the transmission of pressure changes. While this delay is often minimal and acceptable for many applications, it certainly must be considered when rapid control is critical.
The differences in their conductors influence the overall efficiency and responsiveness of the systems, with electrical systems excelling in precision and speed, while pneumatic systems, despite potential delays, showcase adaptability in diverse and complex automation environments.
Adjustability: Controllers vs. Valves
The disparities between electrical and pneumatic systems become evident with the transitions through the actual control elements. Even for basic control, electrical systems employ switches, relays, and transistors to modulate the flow of current. For instance, switches can open or close circuits, relays can control multiple circuits based on a single input, and transistors can amplify or switch electronic signals. These components enable fine-tuned adjustments in the operation of actuators, ensuring accuracy in various industrial processes.
Pneumatic systems use valves to regulate the flow of compressed air, introducing a more gradual response due to the compressibility of air and the mechanical motion needed toopen a valve port. While flow control valves in pneumatic systems provide control over the release of energy, the inherent characteristics of air compression introduce a potential lag in response.
These differences in valve-based control mechanisms again influence the overall speed and responsiveness of the two systems, with electrical systems again excelling in quick adjustments and pneumatic systems providing controlled, but potentially slower, energy release.
Electrical vs. Pneumatic: Which One is Better?
The selection between electrical and pneumatic control systems hinges on the requirements of a given industrial automation application.
Electrical systems, with their use of wires for rapid signal response and switches for immediate control, are well-suited for applications where accuracy and speed are paramount. On the other hand, if the environment involves heavy-duty operations in challenging conditions where durability and reliability take precedence, opting for pneumatic systems becomes the more prudent choice.
The decision should be guided by a comprehensive understanding of the specific demands of the application and considering factors such as precision requirements, environmental conditions, and the desired balance between speed and ruggedness.
RELATED CONTENT
Types of Actuators: Comparing Pneumatic vs. Electric Actuators
Deep Learning Simplifies Electric Vehicle Battery Inspections
Improve Electric Drive Control & Efficiency with Adaptive Computing
Introduction to Pneumatic, Hydraulic, and Electric Actuators
An Introduction to Track Conveyance Systems