By Eric Whitley, L2L in CONTROL AUTOMATION
The Importance of Real-Time Data
For Industry 4.0, real-time data has become the currency of operational excellence. Connected worker platforms amplify the value of real-time data by integrating it into a centralized system. Various stakeholders, from machine operators to top-level management, can access and act upon the data.
It's not just about collecting data anymore — it's about collecting it in real time and making it actionable within an instant.
This represents a paradigm shift from the days when data was something you hoarded all week, only to analyze it during a Monday morning meeting for future decision-making. Now, you can take advantage of immediate feedback loops enabled by connected worker platforms that allow for on-the-spot adjustments.
The importance of real-time data extends across various facets of manufacturing, from quality control and equipment monitoring to the execution of complex tasks. These tasks often require a level of precision and timing that only immediate, actionable data can provide.
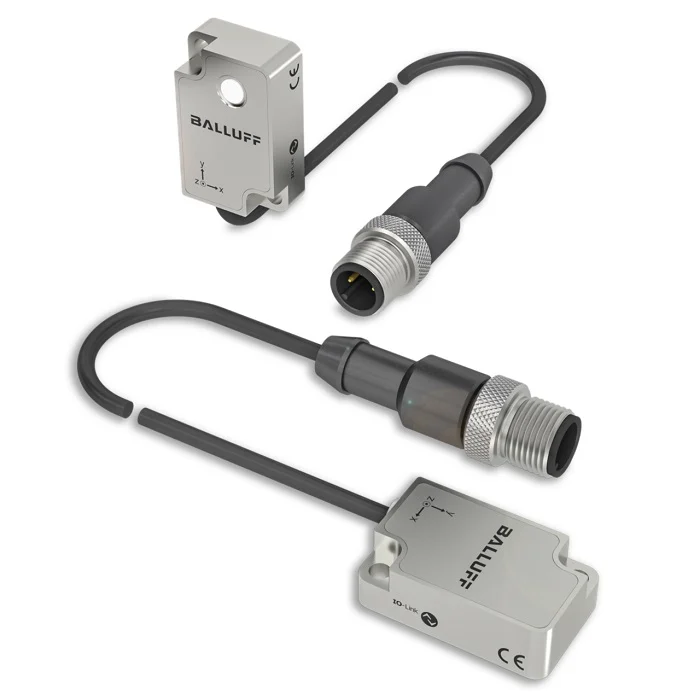
Figure 1. Example of a condition monitoring sensor. Image used courtesy of Balluff
Challenges and Solutions
Implementing sensors in a manufacturing environment is not without its challenges. From data security to sensor calibration, there are several hurdles to overcome:
Sensor drift: Over time, sensors can lose accuracy. Regular calibration should be part of your maintenance schedule.
Data security: A compromised sensor can bring down an entire operation. Invest in multi-layered cybersecurity measures, including data encryption and secure access controls.
Integration issues: Sensors from different manufacturers often have compatibility issues. Opt for sensors that comply with industry standards like OPC-UA to ensure seamless integration.
While challenges exist, they are far from being insurmountable. Proper planning and following best practices will enable you to leverage the full potential of sensor technology.
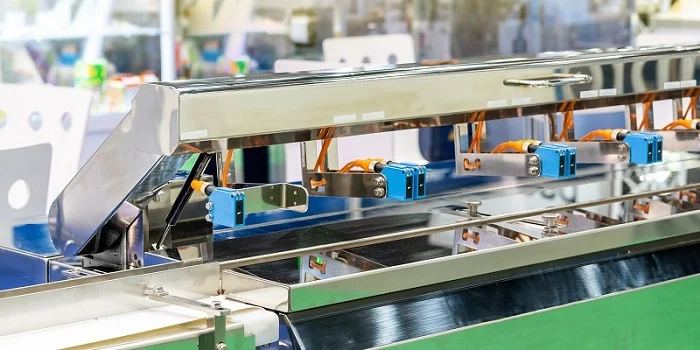
Figure 2. Sensors on a conveyor line. Image used courtesy of Adobe Stock
The Future of Sensor Technology
As we stand on the threshold of a new technological era, the buzz is all about quantum sensors and edge computing. They're the next logical steps in the evolution of sensor technology.
Quantum sensors, for instance, offer unprecedented sensitivity and accuracy, opening doors to applications we've only dreamed of. Edge computing allows for quicker data processing right where it's generated, reducing latency and enhancing real-time capabilities.
The endgame, however, remains the same: to derive actionable insights that can be immediately applied to improve operational efficiency and product quality. These new technologies should serve to enhance our existing systems, making them more robust and responsive, rather than being an end in themselves.
Sensors have evolved from mere data collectors to become the cornerstone of modern manufacturing. They're the eyes and ears of the factory floor, constantly feeding the data ecosystem.
If you're not already integrating advanced sensor technology into your manufacturing processes, you're actively moving backward. The future is sensor-driven, and it's time to get on board or risk being left behind the competition.